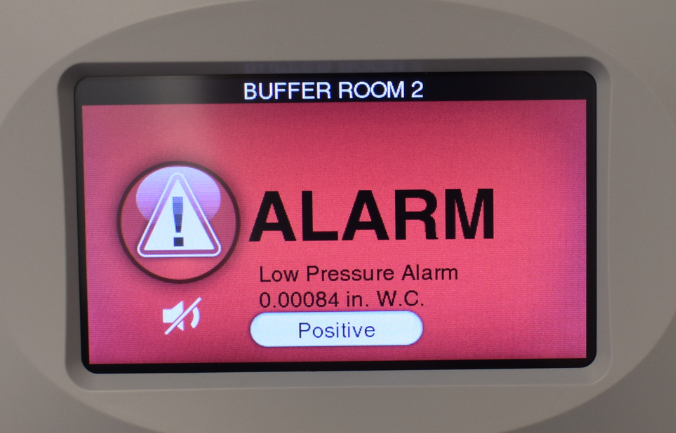
By Adam West, Course and Curriculum Manager at CriticalPoint
When to Certify
USP <797> states that, before a pharmacy can begin sterile compounding activity, the pharmacy cleanroom and devices must be certified initially and every six months thereafter. Simple. Done and done. Right? Well, maybe not so simple. As in other sections of USP, holes still remain in certification language; and in some areas of the chapter, there is room for interpretation. Despite the surprising and disappointing removal of CETA’s Certification Guide for Sterile Compounding Facilities (aka CAG:003 – 2022), there are still a few details and scenarios around the topic of cleanroom certification and recertification that provide the specifications we need.
The art of cleanroom certification is fascinating in more than a few ways because there are so many diverse circumstances. Everything is different yet, somehow, still the same all at once. Certification is not a cookie-cutter process. Yes, testing standards and guidelines are created to ensure a uniform, repeatable, and accurate result. But I’m talking about the different design specifications, manufacturer brands, air handlers, and all the quirks. Experiencing the challenges and hard times during those late nights at customer sites is what shapes a great certifier (but I digress).
No one facility is the same as another, even if they appear to be alike. Airflow design and parameters vary between sites as much as they do for identical biological safety cabinets (BSCs) located side by side. With that said, does your facility remain certified until it’s due for recertification? It depends on what happens during those six months.
Do we need a more frequent certification schedule?
No. Well…maybe. In a perfect world, if the facility parameters (the mechanical setpoints that maintain the airflow design specific to your facility) never change, or aren’t disrupted, or haven’t experienced a loss of power or performance in that six month span, then certification is only required at the next routine frequency. That next certification testing interval ultimately will reveal if anything has changed or if it has stayed the same and will pass certification.
However, there are circumstances where recertification is required based on certain scenarios described in USP <797>. The chapter states that “…areas additionally must be recertified if there are changes to the area such as:
- redesign
- construction
- replacement or relocation of any primary engineering control (PEC)
- or alteration in the configuration of the room that could affect airflow or air quality.”
This list is fairly comprehensive regarding situations that require recertification. However, the term “construction” is too general in my opinion. There are some activities that fall under the construction umbrella but really don’t affect the configuration of the room or its air quality (maybe temporarily). I know I’m not the only one who struggles with deciding what actions would require recertification. There are nuances not covered in the chapters, and certification isn’t cheap, right? No, I don’t think repairing some wall damage falls under the type of construction that requires recertification. While repair and painting interfere with actual compounding activity, it does not disrupt airflow behavior or airflow delivery systems such as the HVAC controllers.
Another frequently confusing scenario is moving the PEC around the room during cleaning activity. Most folks understand this is a necessary step in executing proper cleaning protocol and does not require recertification. We can temporarily move the PEC to the side to clean and move it back without fear. The chapter means that, if your PEC was placed along the east wall of the room and you now want to relocate it to the west wall of the room, the dynamics and airflow efficiencies of that certified environment have been potentially disrupted or could negatively impact the room’s ability to exit airflow and contaminants effectively. Therefore, it’s a new room dynamic that has not been certified/verified to confirm that the changes made are suitable for sterile compounding activity.
What scenario requires recertification?
According to USP <797>, it is up to the designated person (DP) to decide—more like decipher—when recertification is necessary. In the event of power loss, things that are already bad can get worse. The mechanical setpoints can go wonky and not return to normal conditions when power is restored. Or the system just turns off like a light switch and powers up the same way as if nothing had happened. Often, the only way for the DP to know or be able to tell if the system returns to “normal” is by checking the only tool they have that provides real-time data: the pressure monitoring systems staged in the rooms they monitor. Since these devices already require a daily review on days when compounding occurs, it’s easy to trend and know what “normal” is for your specific facility. But is that a fail-safe method? No, not if it falls under the “things just got worse” category.
If the pharmacy cleanroom mechanicals and air quality did not properly restore, would you know? Maybe, but you likely only have the pressure monitoring data to assess the situation. You could also request (from the facilities department) a system performance check on the air handling system to verify that the speed parameters and valves are operating as designed. But air is invisible. If something is wrong, you may not find out until viable air monitoring reveals unusual results (alert or action levels) or at the next routine certification. Aren’t cleanrooms fun?
When is recertification really, really required?
Outside the chapter-provided scenarios and your professional judgment, there is one point I’d like you to leave with: A routine certification interval verifies and certifies that the room (and ISO 5 devices) is operating as designed. This certification session is what qualifies the air quality and parameters for the next 6 months (at the time of test) UNLESS something unforeseen happens to the HVAC system within that interval. If there are any adjustments made to the air handling system within the current certification interval that derived from poor performance in pressure or airflow, the current certification certificate is void because changes have been made to the original certified airflow parameters that were tested.
If you request that the HVAC system be evaluated, facilities teams may not know to provide you all the details of what was done to get the system back to design. The facilities team and/or air balance vendors MUST tell you how and why “everything is fine now.” Additionally, being told “we made an air handler adjustment” simply is not enough to inform you of the how and the why of what happened for your investigation of the issue. As part of that investigation and remediation plan, adjustments made to the system require certification of the new system design and cleanroom air quality. This is because the airflow has likely been balanced, increased, or decreased from its previously certified setpoints. In other words, it is altered from the certified design.
CriticalPoint Recommendations and Best Practices
Be vigilant in understanding your cleanroom AND the HVAC control systems powering it. This is easily achieved by establishing a good working relationship with your facilities team. Many pharmacy folks have had wonderful results by doing this. But be sure they inform you when and how something is adjusted or changed. This will give you the ability to decide if the engineering controls need to be recertified, as these changes may have voided the current certification.
If you’re experiencing a “things just got worse” scenario, USP requires the DP to begin a formal evaluation of the impact on air quality, investigation of the system, and corrective actions taken to return to proper compounding conditions. It is critical that any departments or vendors relay important information and factors about the HVAC system repairs to you so that you can include them in your corrective and preventative actions (CAPA) report.
CriticalPoint recommends that certification and air balance vendors are scheduled together if significant changes are required to return the system to design. Remember, these vendors are not the same and do not always perform the same work. An air balance report does not replace a certified environment certificate.
Lastly, full certification is not always required. DPs are required to evaluate and confirm the air quality of the compounding environment. HEPA filter leak testing may not be required provided they remain unharmed when things get worse. All you may need are particle counts and verification of the air changes per hour (ACPH) and pressure differentials.
Click here to learn more about the valuable training we provide to pharmacy staff who are designated persons.
View our Best Practices for Nonhazardous Sterile Compounding + Designated Persons Course