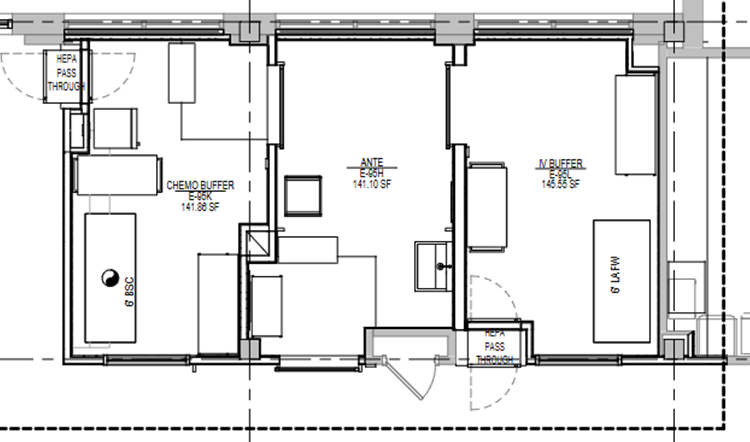
By Adam West, Course and Curriculum Manager at CriticalPoint
I don’t have a fancy mudroom, but I do have a garage that is attached to my house through a neatly decorated lounge area. It’s one of the only rooms that stays clean and organized because it’s hardly ever used. I’ve noticed something about this design: The more the garage is kept clean, the less is tracked into the lounge area.
The rain, snow, leaves, dogs, and kids can make it a real challenge. But the correlation I want to make is between cleanroom design and the general cleaning that maintains the areas outside the suite.
A few years ago, I was tasked with determining the root cause of the repeated microbial excursions in a modular cleanroom located in the back of a warehouse. The space was separated from the main offices, which had carpet and regular ceiling tiles. However, the space had two access points with unrestricted foot traffic. One entrance led to a busy shipping department with a constantly opening bay door, while the primary door led to the office areas.
Here’s what I discovered:
Restrict entrance and exit points of the surrounding areas
This pharmacy had a dedicated controlled nonclassified (CNC) area just outside the cleanroom structure. A nice feature if you have it—but detrimental to your cleanroom microbial state of control if you don’t understand its relationship to the cleanroom. The first major issue was the entrance to the shipping area, which had no physical door. Installing a door was critical to controlling the CNC environment and keeping out adjacent contamination. The primary office door was overrun with staff going in and out freely. An operational workflow assessment revealed a way to reduce the amount of foot traffic to the CNC area without impacting daily work activity— restricting the door to badge-access personnel only.
Properly store bulk supplies and materials
The CNC area had an excessive storage and boxes. There was a catchall corner where years of clutter had accumulated. In another corner, supplies were staged just outside the entrance of the cleanroom that was dedicated to supply storage.
No cardboard was present in the cleanroom, but towers of it littered the CNC area. All evidence that lead to particle generation, dust, and contaminants creeping into the cleanroom entrance. Despite being under positive pressure, the pressure is lost when doors are opened, and the cleanroom “inhales” a burp of the adjacent environment. It’s just one of many ways contaminants are introduced into the cleaner environment.
This is unavoidable, and you hope that the cleanroom design is stout enough to take that temporary burp of contamination and dilute it or remove it from the room through returns and doorway undercuts via airflow pressures. But in this case, the outside environment was so polluted that the cleanroom couldn’t fight off the mass contamination coming in. We resolved this by relocating unnecessary items stored in the CNC. This opened up the space substantially but also revealed other issues: dust, bugs, and debris.
A clean and tidy CNC for cleanroom environmental control
Once the clutter was removed and doorways restricted traffic and outside environmental elements, the CNC was beginning to look like a CNC. However, a cleaning schedule was required to maintain the space. The cleaner the area is outside the cleanroom, the less the adjacent environment can negatively impact the cleanroom’s ability to control ISO classifications. The same is true if your space isn’t a formal and dedicated CNC area separated from other areas.
- Think of the immediate areas around the ingress and egress of pass-through chambers.
- Eliminate drinks, snacks, sweaters, and unnecessary items from the area.
- Consider the flooring type leading to your cleanroom.
- Evaluate the level of cleaning the outer cleanroom area receives.
Synopsis
The poorly utilized CNC area wasn’t the pharmacy’s only challenge to maintaining a successful cleanroom environment. The evaluation also revealed no consideration was given to the number of personnel allowed in the anteroom at one time and that the gowning and hand hygiene practices were subpar.
However, viable sampling showed a quick decline in excursions and out of specification (OOS) results with each process change and improvement. The long-term and sustainable effects were better cleanroom air quality and a host of experiences the staff won’t forget as we journeyed together getting this cleanroom environment consistently performing as intended.
Want to view all of our blogs all in one spot? Access our entire Chronicle library here!
Learn about CriticalPoint’s product offerings!
Related Resources
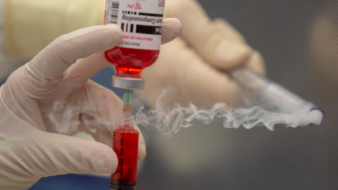
The Compounding Chronicles: Are Smoke Studies Still a Thing?
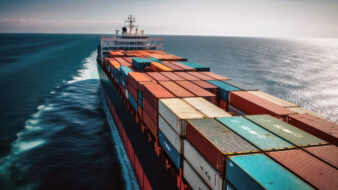
The Compounding Chronicles: Outsourced Suppliers and Shortages and Tariffs, Oh My!
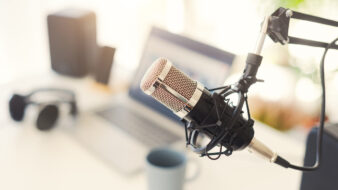