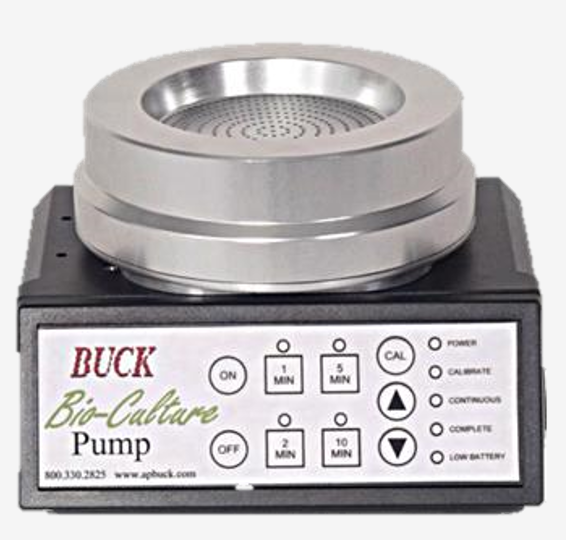
Image courtesy of A.P. Buck Inc.
By Adam West, Course and Curriculum Manager at CriticalPoint
Whether you are a pharmacy team member responsible for performing viable air sampling or a field certification technician, there are several options when choosing an air impaction sampler. Most selections are determined by cost, efficiency, and availability. There are top-of-the-line brands that offer a host of benefits from routine service perks to durability. But users also favor convenient, middle-of-the-road options that provide the same result: 1,000 liters of air sampling. Sample-time efficiency and how fast we get there via sample rate—typically 100 liters per minute (LPM), 180 LPM, or even 200 LPM—is another consideration.
100 LPM sampling devices take 10 minutes to complete a single sample location (100 LPM x 10 minutes = 1,000 cubic liters), while 180 LPM sampling devices finish in just under 5-½ minutes, meeting USP’s minimum sampling requirement of 1,000 cubic liters. For higher or lower sampling rates you must consider the D50 value associated with the manufactured brand to determine if the science supports the impaction rate and your needs for viable air sampling.
In this month’s blog, I’d like to raise awareness of the idiosyncrasies and key performing characteristics of a popular air sampling unit: the Buck Bio-Culture™ Pump. This is based on my anecdotal experience and from following the recommended operation instructions provided in the Buck’s quick guide manual.
Always Read Instruction Manuals
It’s important to read the manufacturer’s service or operation manual in order to fully understand the equipment you work with. This is true even if the piece of equipment is inherently easy to figure out or operate without an instruction manual. Otherwise, certain elements of operation and care can be missed. This could result in less-than-optimal performance in the sampler and inconsistencies in microbial recoveries. Therefore, the results from viable sampling aren’t appropriately represented and could be inconclusive to determine a suitable microbial control.
Let’s Talk Calibration and Frequency
I review countless pharmacy documents each year regarding certification and viable sampling. And I always wonder what “calibration” means when I see a Buck Pump listed in the calibration records.
Most calibrated items, including popular air impaction sampling units, have a one-year calibration frequency. However, the Buck is a little different. For proper calibration, the Buck Pump kit should include a “specially made calibration head” (optional and sold separately), essentially a Magnehelic gauge fashioned with a standard Buck sampling head, which measures the draw of air flow. The Buck calibration head is not used when performing the actual air sample. It instead verifies the airflow rate of the pump and must be calibrated annually with NIST-traceable calibration standards.
According to Buck’s Quick Guide manual, the Buck Pump itself “should be calibrated once per day for greatest accuracy” using the calibration head unit. This means the calibrated head is used to verify the accuracy of the Buck Pump airflow and facilitate adjustments as necessary using the Buck’s “cal mode” on the device’s keypad. The flow rate adjustment instructions are found in the manual. For this reason, the calibration records should list the daily calibration date for the Buck Pump and the annual date for the calibration head.
When performing the daily calibration steps, 90 mm agar plates should be installed to dial in the appropriate flow rate. This is an important step because all agar media have inherent flow resistance. If a blank plate with no agar media were installed while calibrating, the air flow would exceed the appropriate flow rate and, inadvertently, be too fast when sampling actual media.
Malt Extract Agar (MEA) vs Tryptic Soy Agar (TSA) Media
I have found a noticeable difference in the resistance between TSA and MEA media when calibrating the airflow rates using the calibration head. I detected that MEA plates needed higher airflow parameters to achieve the desired flow rate and attain the proper 100 LPM flow rate according to the manual’s calibrator chart. This is likely because the media density for MEA is greater than that of TSA. When sampling with both TSA and MEA media, my recommendation is to use two Buck samplers (one per media type) and calibrate the desired flow rate for the specific media used. Otherwise, you’ll need to adjust the flow rate each time you switch between TSA and MEA.
I want to emphasize the importance of allowing agar media to acclimate to room temperature. The density of media is greater when cold. So not properly allowing the media to adjust to room temperature can affect the flow rate and backpressure of the Buck unit.
Synopsis
USP <797> requires a minimum of 1,000 liters of air for impaction units. You must select an appropriate air sampler to achieve this compliance requirement. However, consider the functionality of the selected device and follow all manufacturer recommendations for proper operations. Air samplers are designed to reach 1,000 liters, but how they are designed to get there matters. You must understand how your device is designed and operates to maintain accuracy when confirming whether your environments meet a proper microbial state of control.
Want to view all of our blogs all in one spot? Access our entire Chronicle library here!
Learn about CriticalPoint’s product offerings!
Related Resources
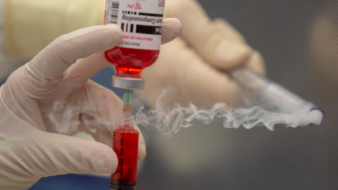
The Compounding Chronicles: Are Smoke Studies Still a Thing?
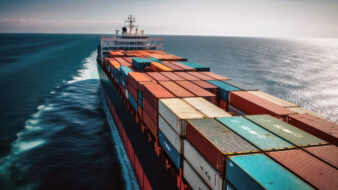
The Compounding Chronicles: Outsourced Suppliers and Shortages and Tariffs, Oh My!
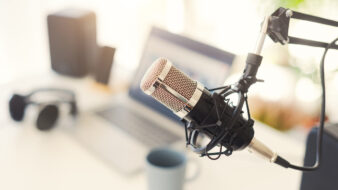