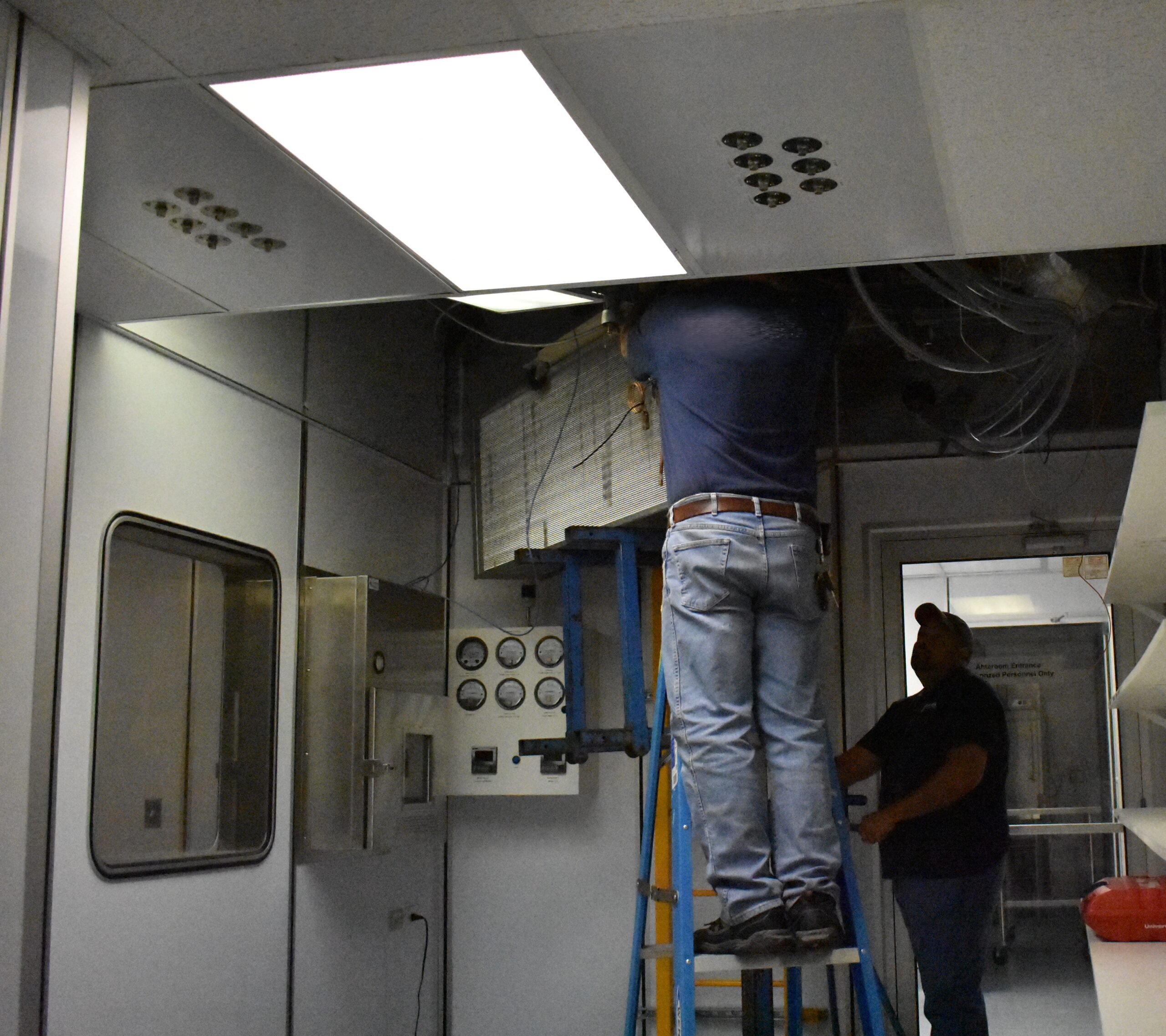
By Adam West, Environmental Monitoring and Training Specialist at CriticalPoint
In our last power loss blog, I discussed the importance of planning for the unexpected when it comes to the engineering controls of the pharmacy cleanroom and compounding equipment. However, there are a myriad of elements that designated persons (DPs) must examine if they want to return to compounding activity efficiently and effectively. In part two of our Surviving Power Loss blog series, we cover different high-level topics to consider when unexpected power loss occurs.
Was any other critical equipment affected?
If yes, a DP responsible for quality must be notified to inspect equipment and determine if operational criteria are still meeting the expected parameters. Recalibration and service may apply in this situation, which can take time and planning to complete. If refrigerators, freezers, and/or incubators experienced power loss too, not only will return-to-normal operations need to be confirmed, but the contents inside these devices require evaluation as well (e.g., assessing drug storage conditions and temperatures, conducting visual inspection). DPs must determine if drug quality was negatively influenced during the power loss.
Is cleaning necessary before resuming compounding activity?
Cleaning is inevitable after power loss is restored. However, the level of cleaning depends on the duration of the power outage and the stability (confirmed through recovery testing) of the cleanroom suite conditions once restored. During an outage, your pharmacy cleanroom has lost some level of microbial state of control and controlled environment specification. This means that surface cleaning and disinfection are expected prior to resuming compounding.
We traditionally use the over/under-1-hour time span to determine the level of cleaning needed before resuming activity; but let me remind you, excursion data is still paramount to determining forward action after power loss.
If power is restored in less than 1 hour:
- Remove all items from PECs. Perform PEC cleaning using a sterile EPA-registered one-step sporicidal agent followed by wiping with sterile 70% IPA after appropriate sporicidal dwell. If any of the PECs are C-PECs, then perform appropriate decontamination, cleaning and disinfection, and wiping with sterile IPA. The step of cleaning and disinfection should be performed with a sterile EPA-registered one-step sporicidal disinfectant cleaner.
- Perform daily cleaning activities (easily cleanable horizontal surfaces, high-touch surfaces, and floors).
If power is restored after more than 1 hour:
Perform a triple-clean, which is when all activities in the monthly clean are performed in three separate and distinct applications. CriticalPoint suggests a triple-clean is performed as follows:
Step 1: Clean and disinfect using an EPA-registered one-step bactericidal disinfectant cleaner, ensuring the manufacturer’s dwell time is achieved.
Step 2: Clean and disinfect using an EPA-registered one-step sporicidal disinfectant cleaner (agent of choice for monthly cleaning) and ensure dwell time is achieved.
Step 3: Clean and disinfect again with the same sporicidal agent used in step 2. The sporicidal agent is used twice to ensure all surfaces have come in contact with the agent. When cleaning furniture and large room surfaces, skipped spots occur even when the agent is applied carefully.
Step 4: PECs must be cleaned three times as well using sterile cleaning and disinfecting agents; however, the last step is always to wipe all surfaces with sterile IPA to remove residues and further sanitize.
Other considerations when preparing for power loss
- Having a power loss SOP and an action list is a MUST!
- Perform a facility-shutdown qualification study.
- Consider backup generators for cleanroom suite AHUs and other critical equipment.
- Don’t operate 24/7? Consider installation of continuous monitoring systems for all critical equipment.
Be prepared with facility shutdown SOPs based on data collected from room recovery tests and qualification studies. In addition, the equipment can be affected by power loss, and the activity level can be affected by the halt in operations. Rank equipment and actions based on how critical they are to your pharmacy ops. Lastly, document, document, document! Inspectors will want to know what was done during and after the power loss.
Want to improve your sterile compounding practice and be prepared for unexpected scenarios such as power loss? Check out our training programs and learn from our team of sterile compounding experts!