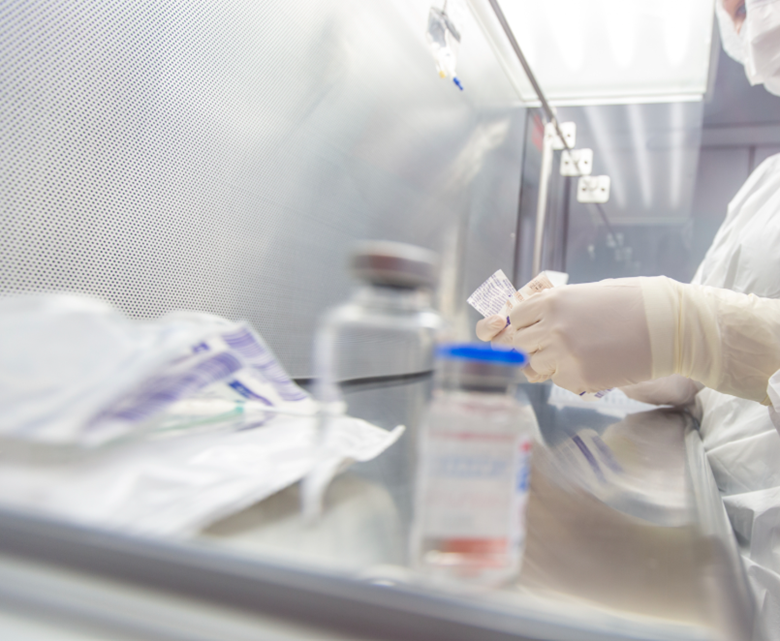
By Adam West, Course and Curriculum Manager at CriticalPoint
Anytime I visit a pharmacy, I inevitably overhear someone declare, “this is my ‘hood” to anyone within earshot. Whether there are two primary engineering controls (PECs) in the room or twenty, everyone knows whose hood is whose in any given pharmacy. And blunt as that may seem, I understand it. You get used to something; you get in a groove. Having to use something different to do the same job can throw off your day.
Is it possible that we carry this odd sense of preference into our sterile competency trainings and evaluations? Let’s say there is a compounding technician who travels to multiple facilities to compound within the same organization. Is there a need to track and perform multiple-location competency forms and training? Maybe. Maybe not.
Multiple-location compounders may not involve multiple competencies
First, before implementing multiple sterile competency policies, evaluate what the operations and workflow look like at each facility. What happens at one location related to garbing and compounding may be very different from what happens at another location. To avoid redundant competencies and training for a single technician at multiple locations, consider a risk assessment and identify the most challenging aspects (risks) at all locations and build them into a primary assessment.
At the very least, this will eliminate the need for gloved fingertip and thumb testing (GFT) and media-fill testing (MFT) for each location. However, it’s important that proper documentation is completed for any staff who travel to multiple locations. The staff member may need to review each location’s policies and procedures, as there may be differences that affect their ability to demonstrate knowledge and competency of core skills, garbing and hand hygiene, and aseptic manipulations. Here is a general list of considerations to get you started:
- What does your state require? It may have specific expectations/requirements regarding competency and documentation.
- Do all locations follow identical SOPs and use the same materials and supplies?
- Do all locations have a similar design regarding the sink location and directives for hand hygiene and garbing?
- Do the facilities share a common design layout and work with the same types of PECs? (Consider vertical flow and horizontal flow ISO Class 5 devices and if the compounders use both interchangeably.)
- How can you build these differences into one primary competency evaluation form?
Cars and PECs aren’t all that different if you think about it
Consider when you’re renting a car. Because you’ve passed a driving test demonstrating you can navigate the roads in a safe and proficient manner, you can essentially drive almost any vehicle you get into. When compounding in a PEC, do we need to take a “driving test” for every “vehicle” that isn’t ours? Of course not.
The important thing to remember is that we aren’t evaluating and qualifying those activities; they are intended for your competency and proficiency value as an individual based on those practices. Pharmacies can sometimes get hung up on the mistaken belief that “I was trained in this PEC, so I have to be evaluated for competency in every PEC or facility I go to.” However, the talent is in you! You take that wherever you go. This is specifically regarding GFT and media fill.
Determining your next steps will be straightforward if you have proper training and competency for garbing and workflow procedures and familiarity with vertical and horizontal flow (as mentioned above).
Provided the compounder is competent in the gowning and gloving process, proficient in sterile compounding techniques with varying PEC designs, and tested on the most difficult and complicated processes, it won’t matter what PEC or facility they perform compounding in. The results of testing and evaluation should always be favorable.
Final thoughts
If you have identical/similar sites with workflow, equipment, and layout, then your assessment details can be quite simple and encompassing for all sites. But if there are differences, you may be able incorporate those challenges into one detailed assessment — that can give you a “license to drive” at any location. Remember the importance of documentation by ensuring varying policies and procedures are reviewed by technicians working at multiple locations to highlight any potential differences in operations and workflow.
Consider our designated persons training course, which will provide application-based opportunities to improve your pharmacy operations.
Want to view all of our blogs all in one spot? Access our entire Chronicle library here!
Click here to learn about CriticalPoint’s product offerings!