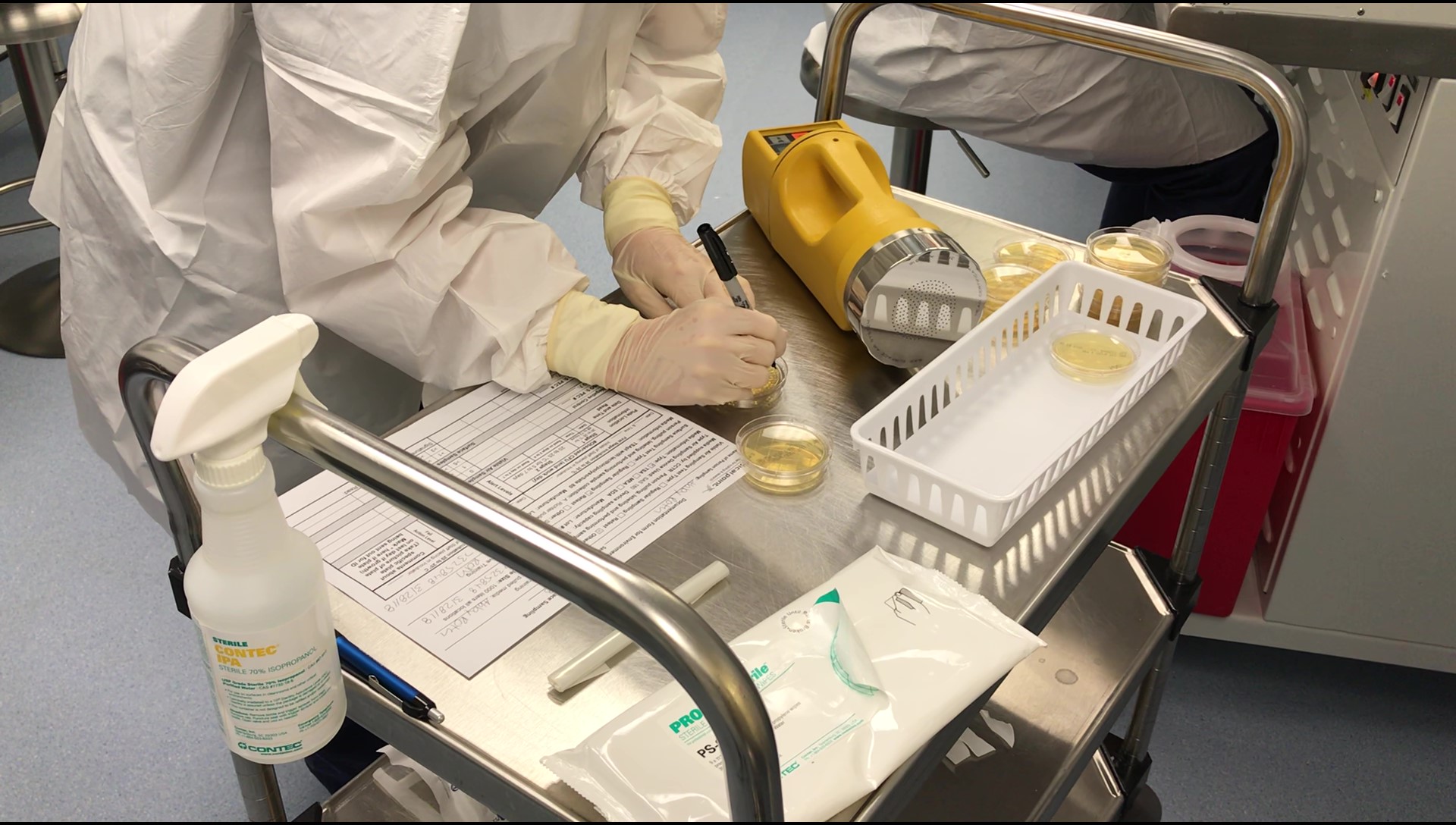
By Adam West, Environmental Monitoring and Training Specialist at CriticalPoint
I’ve been a part of the design, construction, and testing of cleanrooms for 16 years, but my greatest interest is environmental monitoring (EM). Mastering EM sampling is no small feat. And as an environmental monitoring specialist, I’ve known the importance of training field technicians even before it was a thing! Let’s dive into why building USP 797 competency for sample collection in cleanroom environments matters.
Do Your Vendors Perform Environmental Monitoring?
But really, the question should be more specific. Do your vendors have SOPs, proper training, and competency testing in place to perform your viable environmental monitoring sampling?
Did you know that the term “personnel” is mentioned 146 times in USP 797? And it’s used most often to describe the specific function that “personnel” may have. You’ll read examples like “compounding personnel,” “authorized personnel,” “in-process personnel.”
However, one sentence regarding air and surface monitoring immediately caught my attention. USP 797 states, “It is important that personnel are trained and competent in air and surface sampling procedures to ensure accurate and reproducible sampling.” Which personnel exactly? There is no specific context to the term personnel used in this sentence other than stating it is important that personnel who perform air and surface sampling are trained and competent to ensure accurate and reproducible sampling.
I don’t mean to sound like a provocateur, and stay with me on this; we are responsible for ensuring anyone entering the sterile compounding environments performs the proper steps to enter and garb, right? We are also responsible for the safety of our visitors in HD environments.
Environmental Monitoring Recommendations
I recommend that pharmacies dig a little deeper with the services their vendors perform. If we’re held to USP standards based on training, competency, and, most important, quality, why wouldn’t we vet and qualify our vendors to that same level of expectation? Not to mention, our regulators will be digging a little deeper with this year’s inspections to verify we have the proper policies and competencies in place for us.
I encourage you to be prepared. Be vigilant as a designated person to ensure your environments are properly monitored with external services. There are a lot of great vendors out there—even those who may not be as formal as the big national brands that may have all the policies and training in place. Help the industry to become more quality driven by challenging them to be more standard-minded regarding the formality of training and competency.
There’s no entity out there policing vendors. And that’s okay. We need to ensure we receive the best quality of service, and that involves implementing specific vendor qualifications. This can be achieved by asking if they’ve taken the necessary steps to prove they are trained and competent in air and surface sampling procedures to confirm accurate and reproducible sampling.
Are you feeling overwhelmed on where to begin in your environmental monitoring program? Start with us to drive quality and, most importantly, achieve USP 797 compliance with our environmental monitoring training program.